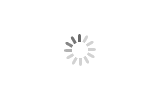
Trailer Brake Pads 29030
Brand FEIROEN
Product origin CHINA
Delivery time 35 days
Supply capacity As your request
1. High quality assurance with EMARK certification.
2. OE quality braking compliant, bringing added safety and reliability.
3. Excellent stopping power
4. Extended pad and rotor life
5. Low noise
6. Consistent braking effort and pedal feel.
7. Wire mesh & adhesive layer provide secure attachment to backing plate.
8. Steel backing plate with corrosion resistant coating.
9. Installation hardware include in every kit.
10. Visual wear slot indicates when brake pads need to be replace.
Front and rear brake pad characteristics
The friction material of the brake pad is a special material that works in a hot and high pressure environment. Therefore, it is required that the filler component used must have good heat resistance, that is, thermal stability, including thermochemical effects of thermophysical effects. Wait. The packing density of the filler has a great influence on the performance of the friction material. The different performance requirements of the friction material also have different requirements for the packing density of the filler.
The Mohs hardness of the brake pad grinding filler is usually 3 to 9. The grinding effect with high hardness is remarkably obvious. 5.5 Fillers above hardness are hard fillers, but the amount and particle size should be controlled. The anti-friction filler is generally a low hardness material, lower than the Mohs hardness 2 mineral. Such as: graphite, molybdenum disulfide, talc, mica and so on. It reduces both the coefficient of friction and the wear of the dual material. Thereby increasing the service life of the friction material.
Early friction plate knowledge
Motor vehicles must have transmission and braking in use, which requires the use of friction plates. The early friction plates were made of cotton, cotton, leather, etc. as a base material, and were processed into brake pads or brake bands. The disadvantage is that the heat resistance is poor. When the friction surface temperature exceeds 120 ° C, cotton and cotton will gradually coke and even burn. As the speed and load of the vehicle increase, the braking temperature increases accordingly, and such friction materials are no longer sufficient for use. So the new friction material - asbestos friction material was born.
Asbestos staple fibers and fabrics and fabrics can be used as the substrate for the friction material. Because of its lower price, it quickly replaced cotton and cotton as the main base material in friction materials. In 1905, the asbestos brake band was applied, and the friction properties and service life, heat resistance and mechanical strength of the products were greatly improved. Beginning in 1918, a combination of asbestos staple fibers and asphalt was used to make molded brake pads. In the early 1920s, phenolic resin began to be industrialized. Because its heat resistance was significantly higher than that of rubber, it quickly replaced rubber and became the main binder material in friction materials. Since phenolic resins are relatively inexpensive compared to other various heat-resistant synthetic resins, asbestos-phenolic friction materials have been widely used in various countries since then.
Brake pad wear
For the car, we all know that the brake system of the car is extremely important for the safety of the car. In the brake system of a car, the braking force is mainly generated by the friction of the brake pad and the brake disc. Therefore, the brake pad is an important part of the brake system, and it is the protector of cars and people.
First of all, the material and structure of the inferior brake disc or brake drum can easily cause abnormal wear of the brake pads. Secondly, the brake calipers of the brake system are damaged for a long period of time, causing the brakes to not return, so that long-term dragging of the sheets and the discs (drums) can also cause abnormal wear. Finally, the materials used for the brake pads are not satisfactory and the design density of the brake pad friction layer is unreasonable, which may also cause abnormal wear of the brake pads. Here to remind everyone, whether it is the brake pads on the disc brakes or the brake pads on the drum brakes, the brake pads on the brakes should be replaced in time to avoid the safety hazard.